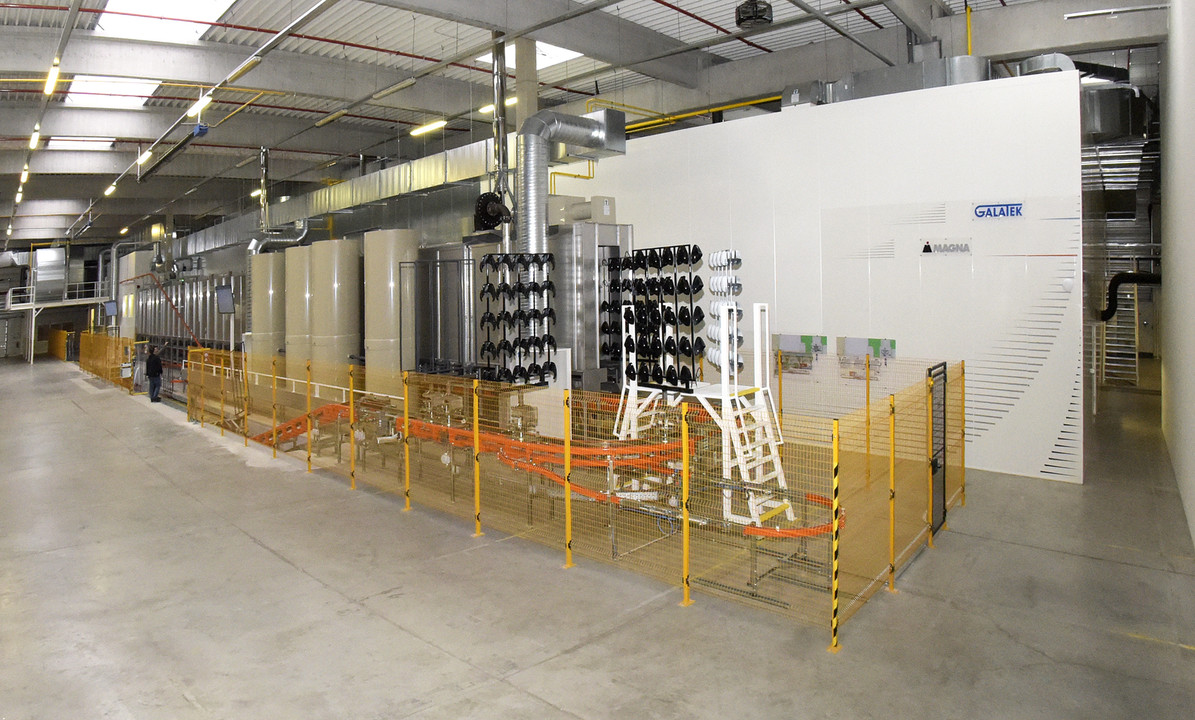
Continuous painting lines are integrated systems of machinery capable of high production, which administer a final treatment to surfaces in either liquid coating or plastic powder form. The process can either be manual or fully automated. Every single line is customised to suit a client’s needs in relation to capacity required, the technological process and the end quality of the coating.
Continuous painting lines vary depending upon the technology requested and are made up of various constituent technological systems. Examples of these are spraying machines for grease removal and phosphatising; devices for electrophoretic painting; booths for applying liquid coatings or plastic powder, which also contain application kits; drying, curing or hardening ovens; as well as volatilisation and cooling tunnels. The surfaces of components treated in the lines are conveyed via various transport methods.
A number of completion systems accompany the delivery of each painting line. Their main purpose is to ensure that high quality levels are achieved by the technological process, and that legislative requirements are observed. These systems include water treatment plants, air handling systems including any necessary moisturizing or cooling of the inlet air, systems for catching or disposing of organic solvents from the exhaust air, stations for producing demineralised water, plants for preparing chemicals and paints, and complex systems for regulation and control of technological parameters of the device. The final design of each particular line is dependent upon the capacity required, the optimised and tested technological process, the demanded quality of the resultant finish, and compliance with the legislative requirements for the operation of the device.
Continuous lines that we have manufactured in the past include various operational plants with differing levels of technological complexity, such as those suited to the demands of automotive or airspace industry.